The countdown to A+Product Awards winners' announcement has begun! Stay updated by subscribing to Architizer's A+Product Awards Newsletter.
“Waste not want not.”
This proverb has long been a favorite of parents and grandparents around the Western world, who are trying to coerce children into eating their dinners. Yet, after taking a second to ponder it, a different sentiment can be gleaned. The proverb’s meaning also precisely describes the fundamentals of a circular economy: use only what you need, and you will never run out. As we struggle with the consequences of our consumerism and our depleting resources, the term has never been more apt.
A circular economy is a leading solution in the fight to eradicate waste and pollution — you may also have heard it referred to as closed-loop, cradle-to-cradle, or zero waste. At its core, a circular economy means that the products we use no longer have the typical life cycle with a beginning, middle and end. Currently, companies and manufacturers are deeply rooted in a linear approach to growth — make, use, dispose. This unaccountable wastefulness has led to levels of product heading to landfill at an unprecedented and unsustainable rate.
Materiality is a key consideration when discussing circular economy. In the design world, materials are typically chosen for their aesthetic and functional qualities. They are selected for their strength and tactility and standard practice dictates that multiple materials are used to manufacture one product. Thankfully, there are swathes of manufacturers who are now taking the onus and using recycled materials for manufacturing their goods. While this may be a great start, there is still more that needs to be done to achieve a closed-loop. What is often overlooked is what happens when a product composed of recycled materials reaches the end of its life. How can it be recycled again?
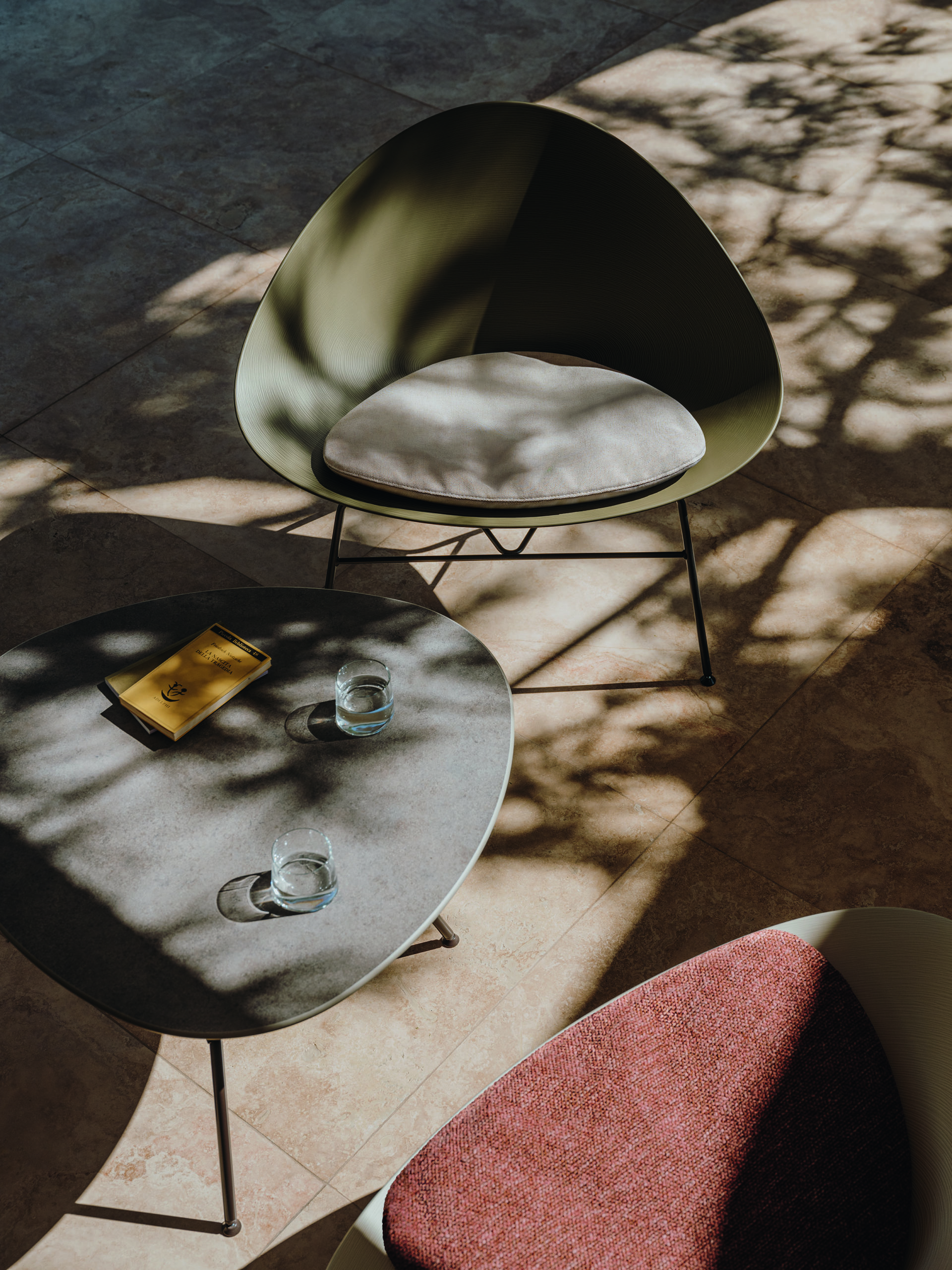
Adell designed Studio Lievore + Altherr Désile Park for Arper, 2021 A+Product Award Winner in Contract Seating
For example, out of 78 million tons of plastic packaging globally, only 14 percent gets collected for recycling, 32 percent leaks into the environment, 14 percent gets incinerated and over 40 percent goes to landfill. Of the 14 percent that is recovered, 4 percent of it is lost in the sorting process, 8 percent gets down-cycled to a material that is of lesser quality and only 2 percent of that 78 million tons can become a material of the same quality as the one it was initially.
When designing Adell — one of their latest pieces for Arper — Studio Lievore + Altherr Désile Park focused on reduction, reuse, and recycling as central pillars for their circular design. The chair is designed with a shell made from 100 percent recycled post-industrial plastic, allowing it to be both recycled and reused. To ensure full recyclability, the designers have used pure materials that can be completely disassembled. Easy disassembly guarantees each component can be separated and recycled individually and contributes to making the chair reusable. It has a flexible component system of shells, bases, and accessories, making it entirely flexible. Flexible products, unsurprisingly, have a longer life span.
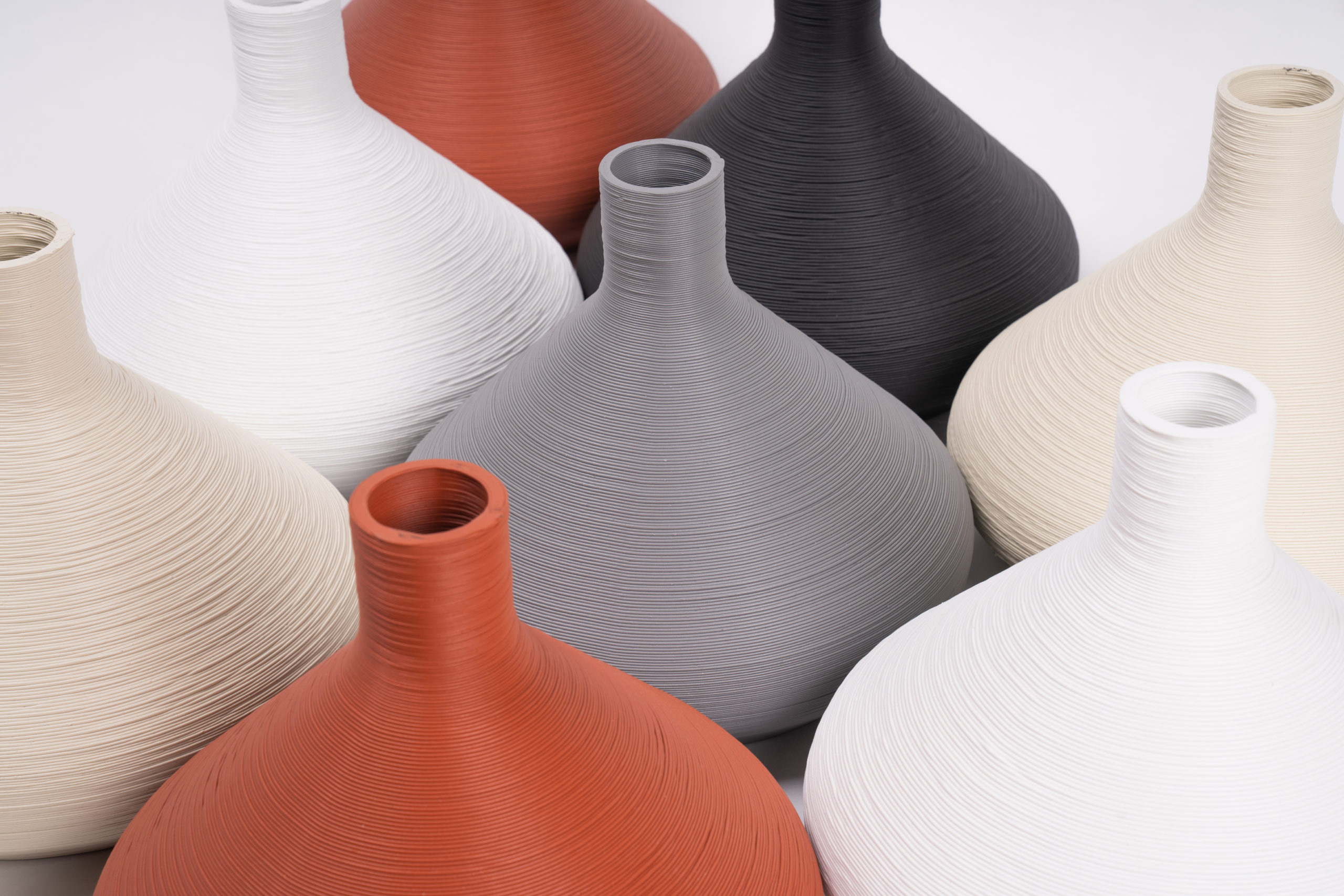
Coil Collection by LightArt, 2021 A+Product Award Winner in Sustainable Design
Every company inevitably produces waste. Particularly those who are in the business of manufacturing. The challenge many designers face is not only reducing waste from the outset but also coordinating how waste produced from their designs can be repurposed. Nestlé famously uses the KitKat biscuits that get broken during production to fill the wafers in new KitKats. This reduces their waste output dramatically.
LightArt has taken heed from the chocolate bar connoisseurs. In their Coil Collection, LightArt take the waste materials from the products they manufacture and by using 3D printing techniques, they have created an entirely new range of light fittings inspired by ceramics. The light fittings are modern, diverse and sustainable. They are helping the business get closer to its goal of Zero Waste manufacturing.
The aspiration for a circular economy is a quandary that has captured the minds of inventors everywhere. It has pushed the innovators in society to question our processes from conception to production and further. It has allowed them to examine what we think we know and to challenge it. Forust Vine 3D Wood Collection by fuseproject (2021 A+Product Award Winner, New Materials) is an example of how technology can flip everything we thought we knew on its head and has the potential to change the design world as we know it.
Until now, wood has not been the most sustainable or recyclable product. Of course, there are ways to make it more so, but, in furniture design, quality wood is revered. Meanwhile, deforestation is at an all-time high and is decimating the planet. Fuseproject may have the answer. Manufactured using 3D printing techniques, Forsut Vine uses sawdust particles to create a material that is as moldable, durable and as beautiful as wood. With strikingly similar properties, the limitations for their new material seem endless.
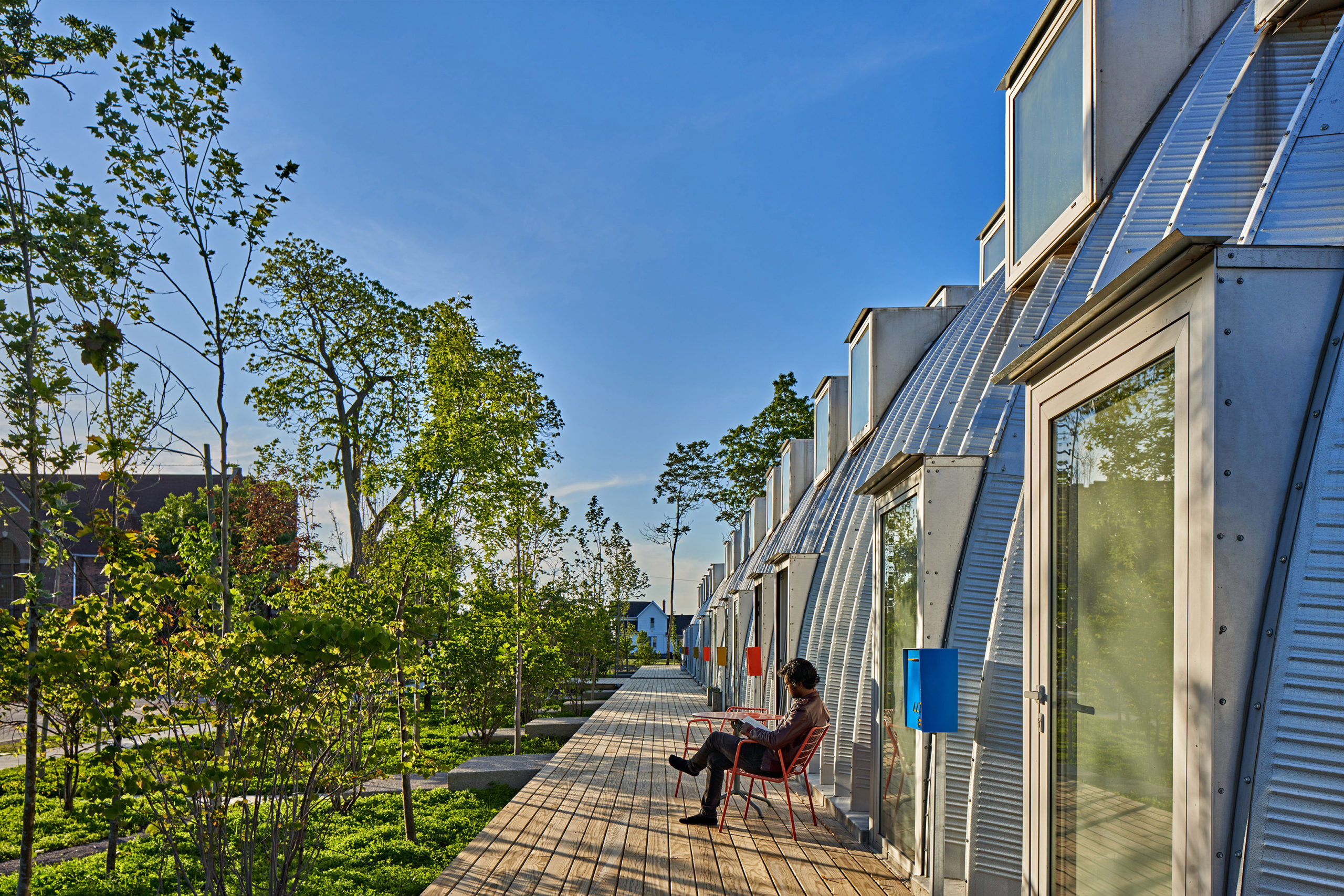
Caterpillar by SteelMaster Buildings, 2021 A+Product Award Winner in Building Envelopes, Cladding, & Roofing
Of course, not all aspirations for a circular economy lie within the properties of core materials. The lifespan of a product can also play a fundamental part in waste eradication. SteelMaster Buildings have looked to tackle the issue from a different perspective. Caterpillar is a prefabricated unit. A beautifully simple and effective prefab structure, it is made from recycled steel that uses 84 percent steel scrap.
More importantly, it can be easily erected and disassembled with a small crew. It is column-less and is designed to be used as any functional space. Its adaptability means that when it has completed its purpose in one location, it can be disassembled, moved or passed on for a new life. In an ideal world, it could live on forever changing location and purpose.
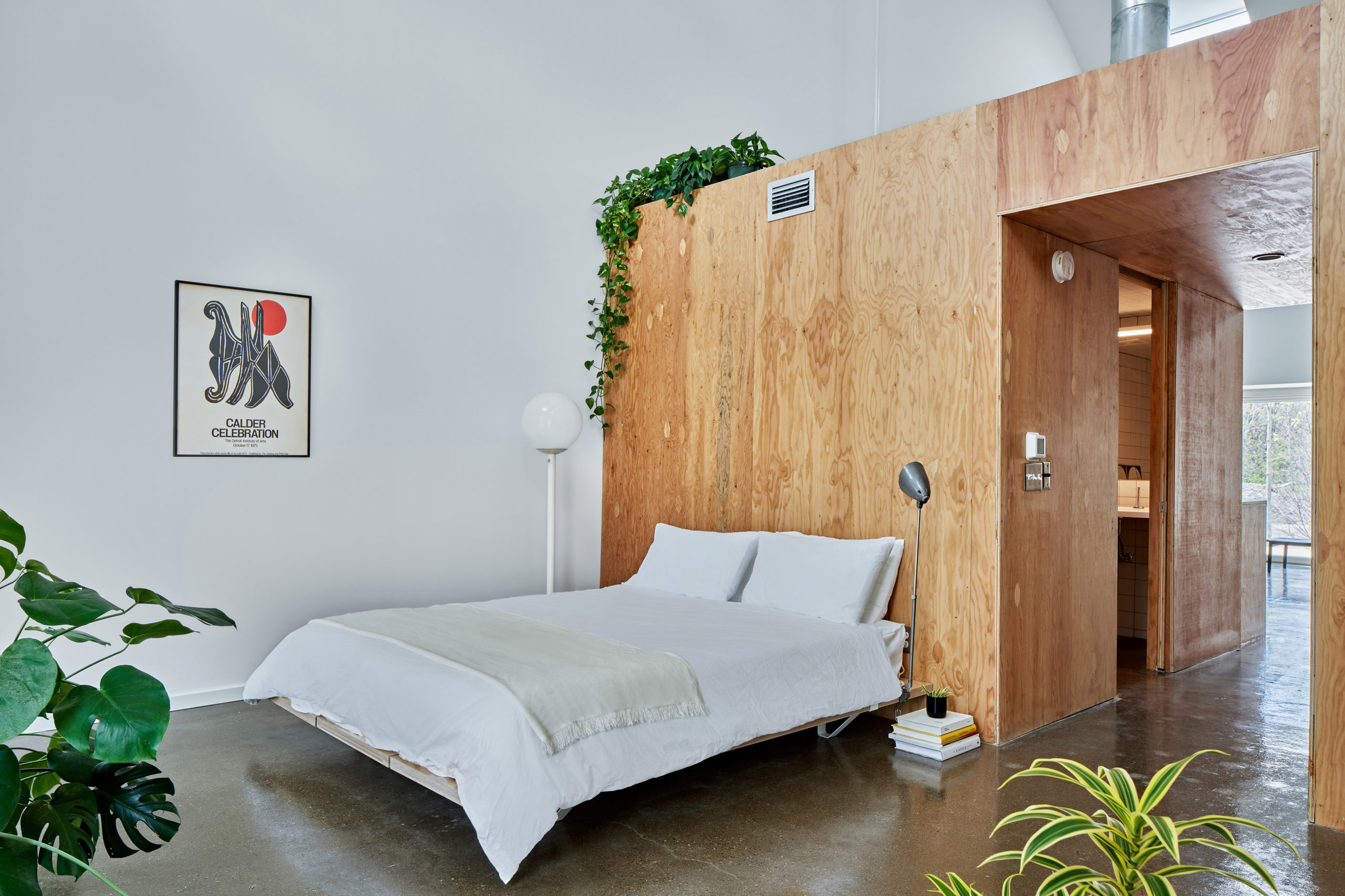
Caterpillar by SteelMaster Buildings, 2021 A+Product Award Winner in Building Envelopes, Cladding, & Roofing
In a circular economy, materials’ economic and environmental values are preserved for as long as possible by keeping them in a closed-loop system. This is only possible if the products’ lifespans are increase, or if they are manufactured in a way that they can be broken down to their core materials to be remanufactured. In this model, the notion of waste does not exist because products and materials are, in principle, reused and cycled indefinitely. There are many ways to adopt circular thinking into design processes, as this collection has shown.
As the idea of a circular economy catches hold, Architizer is championing the innovators, the inventors and the designers who look to make our world a more sustainable place to live for our future generations.
The countdown to A+Product Awards winners' announcement has begun! Stay updated by subscribing to Architizer's A+Product Awards Newsletter.